Implementation of ISO 9001 in the Manufacturing Industry, a Literature Review
- Conference paper
- First Online: 30 August 2022
- Cite this conference paper
- Prashant N. Shende 12 ,
- Aditya Kadao 12 &
- Adithyakrishna Palery 12
Part of the book series: Lecture Notes in Mechanical Engineering ((LNME))
504 Accesses
22,027 International Standards have been produced by the International Organization for Standardization (ISO) (As of Feb 5, 2018). ISO 9000 is one of the most widely used ISO standards. ISO 9000 is a set of quality management system (QMS) standards that give companies and organizations direction and tools to ensure that their goods and services consistently satisfy client expectations, resulting in continuous quality improvement. ISO 9001 is a globally recognized standard for quality management systems. It is an important component of a well-rounded production management system. During a continuous improvement cycle, ISO 9001 helps to simplify the process, increase company performance, and boost efficiency. The case study shows how ISO 9001 was implemented in the manufacturing industry. To better understand the application and advantages of ISO 9001, we conducted a survey in a variety of ways to get input from various industries. Finally, the industry becomes more efficient as all of its processes are linked and understood by all parties involved. This boosts productivity and efficiency while lowering internal expenses. The industry will comply with all legal and regulatory standards. Because some industries and clientele demand ISO 9001 certification before conducting business, the industry can grow into new markets. In a few words, the abstract should describe the substance of the work.
This is a preview of subscription content, log in via an institution to check access.

Access this chapter
- Available as PDF
- Read on any device
- Instant download
- Own it forever
- Available as EPUB and PDF
- Compact, lightweight edition
- Dispatched in 3 to 5 business days
- Free shipping worldwide - see info
Tax calculation will be finalised at checkout
Purchases are for personal use only
Institutional subscriptions
Ilkay MS, Aslan E (2012) The effect of the ISO 9001 quality management system on the performance of SMEs. Int J Qual Reliab Manag 29(7):753–778
Google Scholar
Guchu G (2012) ISO quality management system implementation for small to medium manufacturing firms Kenya. In: Proceedings of the 2012 mechanical engineering conference on sustainable research and innovation, vol 4, pp 140–147
Nabavi V, Azizi M, Faezipour M (2013) Implementation of quality management system based on ISO9001:2008 and its effects on customer satisfaction case study. Int J Qual Reliab Manag 31(8):921–937
Keng TC, Kamal SZ (2016) Implementation of ISO quality management system in construction companies of Malaysia. J Technol Manag Bus 3(1):1–21
Almeida D, Pradhan N, Muniz J Jr (2018) Assessment of ISO 9001:2015 implementation factors based on AHP: case study in Brazilian automotive sector. Int J Qual Reliab Manag 35(7):1343–1359
Priede J (2012) Implementation of quality management system ISO 9001 in the world and its strategic necessity. In: 8th international strategic management conference, Procedia—social and behavioral sciences, University of Latvia, Riga, LV-1050, Latvia, vol 58, pp 1466–1475
Download references
Author information
Authors and affiliations.
Department of Mechanical Engineering, YCCE, Nagpur University, Nagpur, Maharashtra, 441110, India
Prashant N. Shende, Aditya Kadao & Adithyakrishna Palery
You can also search for this author in PubMed Google Scholar
Corresponding author
Correspondence to Prashant N. Shende .
Editor information
Editors and affiliations.
Department of Mechanical and Aerospace Engineering, Institute of Infrastructure Technology Research and Management (IITRAM), Ahmedabad, India
Mithilesh K. Dikshit
Mechanical Capacity Building Division, Space Applications Centre, ISRO, Ahmedabad, India
Ashish Soni
Department of Mechanical Engineering, University of Aveiro, Aveiro, Portugal
J. Paulo Davim
Rights and permissions
Reprints and permissions
Copyright information
© 2023 The Author(s), under exclusive license to Springer Nature Singapore Pte Ltd.
About this paper
Cite this paper.
Shende, P.N., Kadao, A., Palery, A. (2023). Implementation of ISO 9001 in the Manufacturing Industry, a Literature Review. In: Dikshit, M.K., Soni, A., Davim, J.P. (eds) Advances in Manufacturing Engineering. Lecture Notes in Mechanical Engineering. Springer, Singapore. https://doi.org/10.1007/978-981-19-4208-2_27
Download citation
DOI : https://doi.org/10.1007/978-981-19-4208-2_27
Published : 30 August 2022
Publisher Name : Springer, Singapore
Print ISBN : 978-981-19-4207-5
Online ISBN : 978-981-19-4208-2
eBook Packages : Engineering Engineering (R0)
Share this paper
Anyone you share the following link with will be able to read this content:
Sorry, a shareable link is not currently available for this article.
Provided by the Springer Nature SharedIt content-sharing initiative
- Publish with us
Policies and ethics
- Find a journal
- Track your research
Choose your region and currency
Get Certified
ISO 9001 Certification Process
Learn how to quickly implement a business-friendly ISO 9001 system.
Guided DIY Toolkit
Full-Service Consulting
Hybrid ISO 9001 Certification
Maintain & Improve
How to Improve Your QMS
Turn your underperforming ISO 9001 system around.
Documentation Templates
ISO Consulting Service
ISO Internal Audit Service
Document Review
Training Recommendations
Find the ISO 9001 training course you really need.
Online Training
Custom Training
Video Courses
Learning Center
A wealth of information on everything ISO 9001.
Case Studies
Free Downloads
Registrar Finder
What are you looking for?
HOME / iso 9001 case studies
ISO 9001 Case Studies
Explore our ISO 9001 case studies to witness real-world examples of how companies worldwide have successfully implemented our products to establish custom quality management systems and achieve ISO 9001 certification. These case studies provide valuable insights into the practical application of ISO 9001 and offer tangible proof of the results that can be achieved when utilizing the resources and expertise offered by 9001Simplified.
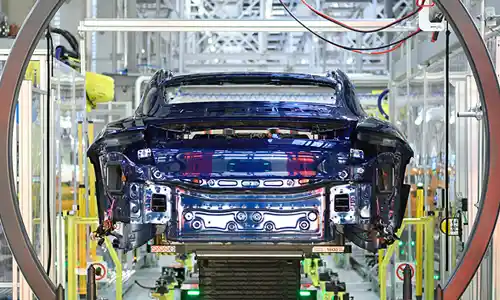
Kingpin Dynamics
Certified: November 2023
Operating as a one-person engineering company in Sweden, Kingpin Dynamics required ISO 9001 certification to increase its appeal to potential clients. Leveraging our DIY Toolkit, the company spent only one month to implement ISO and realize multiple operational benefits as well.
Read the Case Study
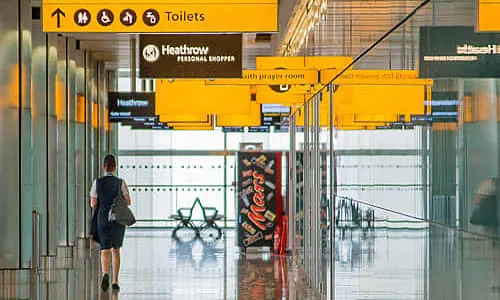
AirportCreators
Certified: March 2021
Located at Schipol Airport in the Netherlands, AirportCreators needed an ISO system that would align with their dynamic and creative culture. With our help, they implemented a lean ISO 9001 system and achieved certification within five months.
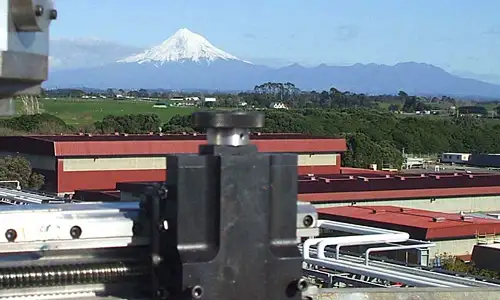
Pace Engineering
Certified: October: 2020
Pace Engineering in New Zealand's South Island wanted to use ISO 9001 to achieve ultimate process efficiency in production and administration. With our Do-It-Yourself kit and training, they implemented a versatile ISO system and got certified nine months later.
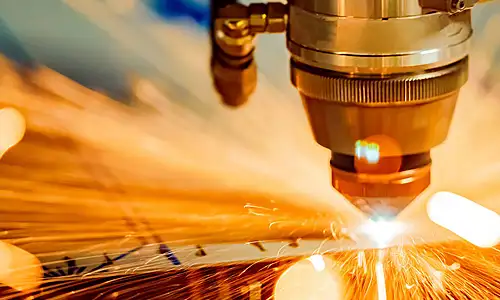
J.T. Fennell
Certified: September 2020
Operating two steel fabrication plants south of Chicago, J.T. Fennell used our products and services to set up an ISO 9001 system that would earn the full support of all employees. They easily passed the certification audit at their first attempt in September 2020.

Copyright (©) 2004-2024. 9001Simplified.com. All Rights Reserved.
How can we help?
Please enter your full name
Please enter a valid email
Please enter a valid phone number
Please enter a message
Send Inquiry
Thanks. Your message has been sent. We'll get back to you as soon as possible.
Looking for information or advice? Ask us anything
We'll reply ASAP
- Advisera Home
- ISO in General
Partner Panel
ISO 9001 Documentation Toolkits
Iso 9001 training.
- Documentation Toolkits
- White Papers
- Templates & Tools
Where to Start
New ai tool.
- Live Consultations
- Consultant Directory
- For Consultants
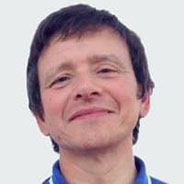
Carlos Pereira da Cruz
- Get Started
How to achieve organizational excellence with ISO 9001: A case study
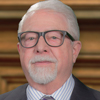
Business leaders are on a continual quest to maximize profits and customer satisfaction. Unfortunately, many see quality management as an overhead expense. If quality professionals are to be more proactive in organizational success, as suggested in ISO 9001:2015 , we need to address Quality Management System (QMS) implementation using a more business-oriented approach. To find out how, read the following ISO 9001 implementation case study.

The paradigm shift – Learn from the industry leaders
The following is a case study of how Dell Computer implemented their ISO 9001:2000 transition. It was first implemented in their Asset Recovery Business (ARB), which had major challenges in meeting its strategic business goals.
The directive was not merely to implement the 2000 revision for compliance, but to examine each element for creating a return on investment. We created a web-based tool called The Business Management Interactive System (BMIS), which was an enterprise-wide operational control system that embedded the requirements of ISO 9001:2000 into the workflow.
The directive from senior management
“ARB will be successful only by focusing on the management system as a whole.
- ISO 9000-1994 focuses on operations related to production and delivery of goods and service
- ISO 9000-2000 scope will require an enterprise-wide focus
The ARB Business Management System will be designed to address current and future management system requirements by incorporating a continuous process improvement methodology across the enterprise.”
Instead of the quality group conducting training for management, management opened the transition kick-off meeting with the following mandate:
- Ever-improving Value to Customers
- Marketplace Success and Enhanced Competitiveness
- Applicable to Entire Organization
- Process-Focused
- Assessments and Measures of Progress Toward World-Class
Implementation
The implementation team consisted of cross-functional individuals who each focused on their own areas of responsibility. A web programmer incorporated not only the QMS requirements, but all business functions into BMIS on the corporate web.
Every piece of data that anyone in ARB needs to do their jobs would be no more than three clicks away.
The screen saver is a scrolling real-time set of operational performance metrics that alerts the process owners to variations in effectiveness and timeliness.
The outcome
And here are the outcomes:
- Within a year of implementation, the division reported that they had turned around a significant operating loss to profitability.
- They were able to create a 40% business growth.
- They increased unit sales by 145%.
- They consolidated five manufacturing facilities into two.
- They reduced manufacturing costs by 15%.
- They reduced out-of-box audit defect rates from 28% to 7.3%.
- Their transition certification auditors praised BMIS as “best in class.”
These are the metrics that matter to business leaders. In this case, they are particularly significant because Dell amortized the cost of our consulting fees and the cost of the employees who worked on the transition in less than a year.
Making the transition
The table below is an overview of the transition from quality management to a business excellence model based on ISO 9001:2015.
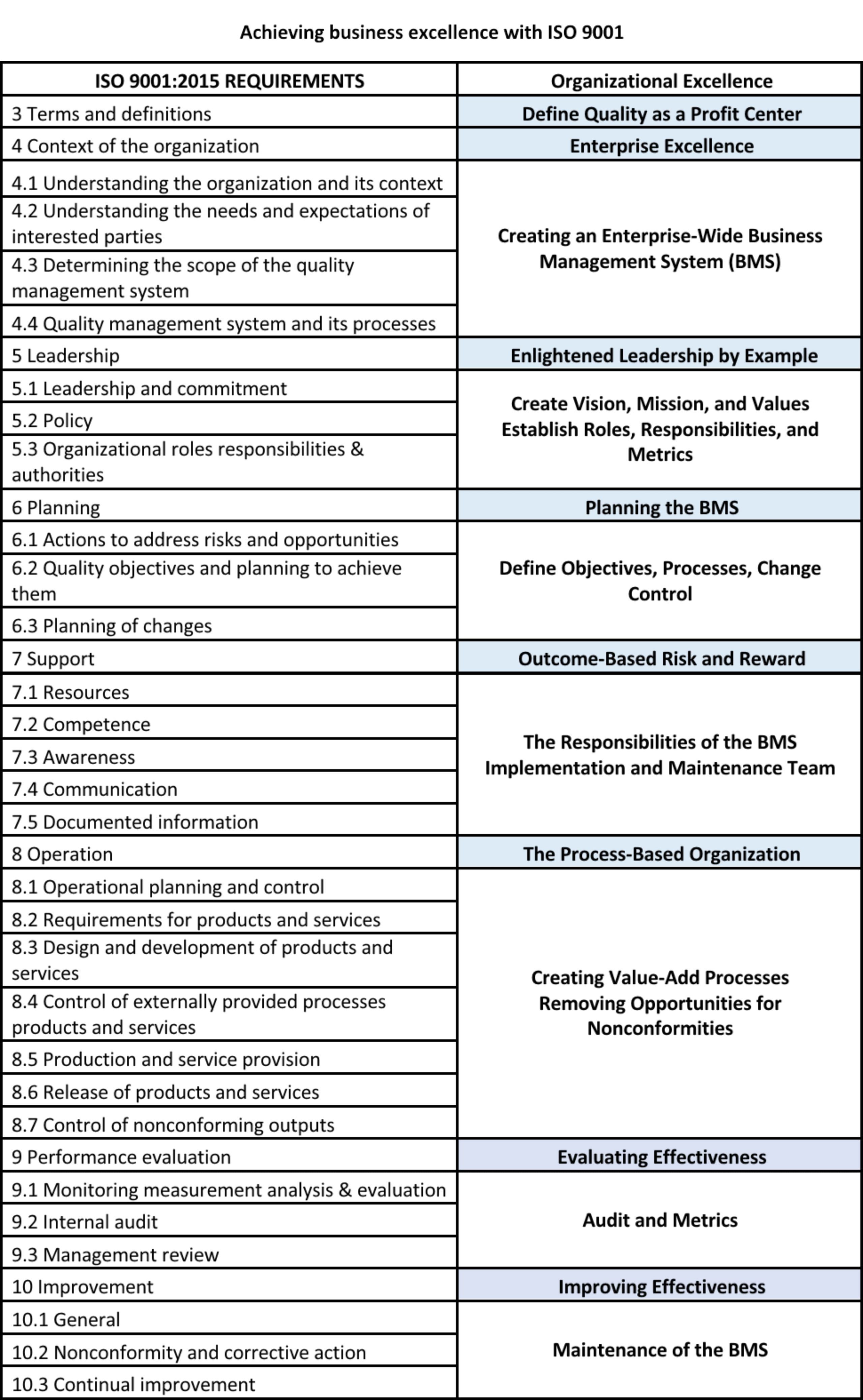
This table is intended to guide the reader into potential enhancements to your QMS if you are striving for a higher level of excellence and greater return on investment.
Meaning of terms
Within the constraints of the blog post, the following are high-level summaries of the meaning of each term used in the crosswalk. Please use the comments section below if you desire more detailed explanations.
- 3.0 – Your organization will need to create definitions of “organizational excellence” processes and tools unique to your environment.
- 4.0 – Beyond the traditional QMS approach to organizational context, identify the contents of the mission and vision you will employ for achieving organizational excellence.
- 4.1 – 4.4 – Consider renaming your management system to Business Management System. It sends a message that the QMS is part of an enterprise-wide model for excellence.
- 5.0 – One of the foundational tenets of highly effective organizations is learning how to lead people and manage processes. Leading creates ownership. Managing people is often punitive.
- 5.1 – 5.3 – In the Dell example, the organization underwent a fundamental cultural renaissance from the top down. This is often not practical in existing organizations, but the traditional quality policy can often be enhanced to create an enterprise-wide mission plan.
- 6.0 – Planning a Business Management System is more holistic than simply implementing ISO 9001:2015.
- 6.1 – 6.3 – Consider a risk-avoidance approach to error-proofing your organization. Focus on identifying opportunities to identify foreseeable risk and include them in your planning.
- 7.0 – Another ambitious undertaking is to consider implementing outcome-based risk and reward metrics for all processes. Encouraging accountability is the basis for defect avoidance.
- 7.1 – 7.5 – If you do not have one, consider empaneling a standing, cross-functional committee to oversee the entire BMS. Conduct regular meetings with specific agendas of maintenance and improvement.
- 8.0 – The ISO 9001-based QMS has always been process-driven. Consider creating similar processes and metrics that do not currently exist in the rest of the organization.
- 8.1 – 8.7 – Within each element of 8, ensure that all process metrics are tied to business key performance indicators.
- 9.0 – Make the focus of improvement more about business excellence than corrective action or traditional process improvement.
- 9.1 – 9.3 – Include risk avoidance and business excellence in the activities of 9.
- 10.0 – Focus on enterprise-level improvement, not just on process improvement.
- 10.1 – 10.3 – There are new paradigms in implementing defect avoidance as a culture, not just nonconformance controls.
For more about ISO 9001 benefits, read this article: Six Key Benefits of ISO 9001 Implementation .
Consider alternative approaches to maximize your business objectives
This blog post is a very high-level introduction to The Evolution of Quality Management to Organizational Excellence. To implement it to the level that Dell ARB did requires fundamental cultural changes, bold risk-taking, and extreme commitment to the mission.
Many of you will find the concept overwhelming. You can, however, implement some of the tenets, like linking quality metrics to business key performance indicators, as a test case. You can become educated on the concepts of leading people and managing processes and gradually facilitate the transition.
For more benefits from ISO 9001 implementation, download this free white paper: How can ISO 9001 help your business grow?
To learn what ISO 9001 certification is, and why it is important, see this article: ISO 9001 Certification .
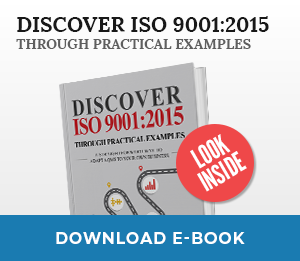
Related Products
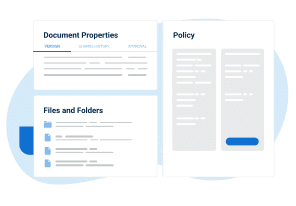
ISO 9001 Documentation Toolkit
Integrated iso 9001/14001/45001 toolkit.
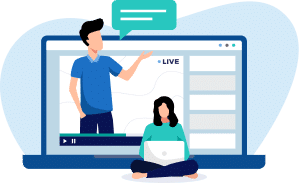
ISO 9001 Foundations Course
Upcoming free webinar.
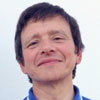
Suggested reading
You may unsubscribe at any time. For more information, please see our privacy notice .
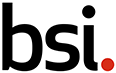
Making excellence a habit
- Verify a certificate
Buy standards

Popular searches
- Lead Auditor Training Course
- ISO 14064-1 Managing Greenhouse Gas Emissions
- ISO 13485 Quality Management System
- ISO 9001 Quality Management
- CSA STAR Certification
Suggestions
ISO 9001 Quality Management case studies

ISO 9001 is the world’s most recognized quality management standard. Implementing the standard can help you to continually monitor, manage and improve quality across all operations. This can help you save money, increase profit, win more business and satisfy more customers.
Read how our customers have benefited from implementing the standard.

Academia.edu no longer supports Internet Explorer.
To browse Academia.edu and the wider internet faster and more securely, please take a few seconds to upgrade your browser .
Enter the email address you signed up with and we'll email you a reset link.
- We're Hiring!
- Help Center
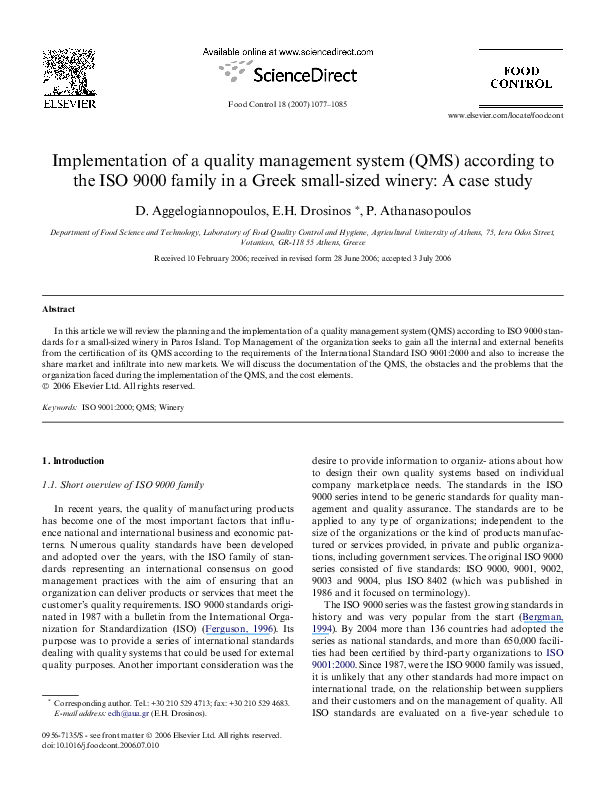
Implementation of a quality management system (QMS) according to the ISO 9000 family in a Greek small-sized winery: A case study

2007, Food Control
Related Papers
Antonio Martin Frutos
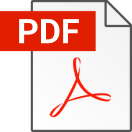
Food Control
Ilija Djekic
Management …
Teofilo Ozuna
Procedia Food Science
Medi Yarmen
IAEME PUBLICATION
IAEME Publication
The manufacturing sector has become the third most prominent segment of Pakistani economy due to its continuous improvement in performance through implementation of the quality management system (QMS). The purpose of this paper is to explore the impact of QMS on the performance of manufacturing concerns of Pakistan. Data was collected from randomly selected employees from the top and middle management through questionnaire survey to check the implementation process and effectiveness of QMS. Results showed that sample companies strictly following the guidelines of ISO standards to enhance their performance. The manufacturing organizations are very much concerned about their performance, so they are continuously improving their product quality. They are maintaining proper evaluation, monitoring and measurement process systems. Customer’s needs and perceptions are also considered by an adequate feedback system, proper audits, and management reviews.
Tudor-George Maruntelu
silvius stanciu
The food industry has a number of Quality Assurance (QA) systems available like GMP (Good Manufacturing Practices), HACCP (Hazard Analysis. Critical Control Points), ISO (International Organisation for Standardisation) standards. These systems and their combinations are recommended for food quality and safety assurance. The agri-food production requires a specific approach to achieve the expected quality level. It is important to know to what extent the systems contribute to the total quality of the product and to balance the tools used for achieving the quality and safety objectives.
Wan Ibrahim
Quality management system (QMS) implementation has been claimed as one of the critical strategy to improve organisational performance. As a major government technical agency Jabatan Kerja Raya (JKR) has taken significant effort to implement QMS with the high expectation to ensure that all project delivered to the clients will meet or exceed their expectation. However recently there have been a lot of criticisms about the ability of JKR to fully reap the benefits of their QMS implementation. These claims seem to have some merit as evidently there are several projects delivered have experience quality problems or even failure. Therefore this study has been undertaken to reappraise the implementation of QMS in JKR. Several issues related to the problems and critical success factors for effective QMS implementation in JKR have been addressed. The methodology adopted for the study includes generating opinion from expert panel and questionnaire survey distributed to JKR personnel and its contractors and consultants. The findings from the study indicated that there is still some limitation in the level of understanding and knowledge in QMS implementation. Various factors to justify this limitation have been identified. Apart from that, the study also identified the factors that can support the development of the strategy for JKR to improve its ability to implement QMS in a more meaningful manner.
Mesfin Mengistu
International Journal of Engineering Applied Sciences and Technology
Pappu Rama Subramaniam
Traditional quality management and monitoring has been shown to be unsuccessful. Today, emerging companies are vying for more value to the consumer in order to ensure their maximum success and sustainability. Many businesses want to ensure that their goods and services are of high quality in order to attract customers. The current situation is implementing quality engineering solutions in industries. Quality engineering is the method of evaluating, handling, designing, and maintaining various systems in compliance with high standards. This method ensures that each stage of the product development cycle is subjected to a thorough inspection by quality engineers, reducing possible losses by eliminating defects from the start. Furthermore, highquality maintenance is important and should be made available for a long time after the product has been shipped. Customers' preferences are shifting significantly, necessitating improvements in design and production technology, which is beco...
RELATED PAPERS
Mohammad Rifky
Ammar HDAIFEH
Food Science and Quality Management
LYDIA AKUNJA
Melek Acikbas Inozu
Victoria Tsolidou
Lang thang du ký
Cyro Barretto
International Journal of Quality & Reliability Management
Jorge Muniz Junior
Universal Journal of Industrial and Business Management
Hamilton Pozo
dspace.thapar.edu
Anita Rajor
Paweł Nowicki
Review of Agricultural Economics
Neal Hooker
Marieta Stefanova
Quality Access to Success
elisabeth siahaan
Scientific works of University of food technologies, University of food technologies Plovdiv
Romulo Sisno
Deepti Chandok
Public Organization Review
Pin-Yu Chu , Chi-Cheng Huang
Journal of Education, Management and Development Studies
JOSE ARIEL IBARRIENTOS
Proceedings in Food System Dynamics
International Journal of Engineering Technologies and Management Research
INTERNATIONAL JOURNAL OF ENGINEERING TECHNOLOGIES AND MANAGEMENT RESEARCH I J E T M R JOURNAL
Ankit Goyal
Andreja Rajkovic , Ilija Djekic
International Journal on Food System Dynamics
Jebreel Jebreel
Vitalis Khaki Basera
SKIREC Publication- UGC Approved Journals
Amalia Serafeimidou
Rufus R Dinrifo
RELATED TOPICS
- We're Hiring!
- Help Center
- Find new research papers in:
- Health Sciences
- Earth Sciences
- Cognitive Science
- Mathematics
- Computer Science
- Academia ©2024

IMAGES
VIDEO
COMMENTS
Quality Management Systems (QMS) & ISO 9001 - Case Studies. Implementing ISO 9001:2015 can help ensure that customers get consistent, high-quality products and services, which in turn can benefit your organization. The following ISO 9001:2015 case studies offer a look at the difference ISO 9001 can make for organizations in terms of process ...
This Implementation Guidance has been developed to assist users in understanding the issues that need to be considered during the co‐existence period between ISO 9001:2008 and ISO 9001:2015. A wide diffusion of this implementation guidance is recommended, in particular the comparison table between ISO 9001:2008 and ISO 9001:2015 matrix ...
The Implementation of a Quality Management System in Accordance with ISO 9001: 2015 Standard: A Case Study March 2022 International Journal of Economics and Business Administration X(1):261-286
I wrote the ISO 9001:2015 Implementation Handbook with the following goals in mind: Provide guidance to organizations (both manufacturing and service) seeking certification to ISO 9001:2015 Assist currently certified ISO 9001 organizations in upgrading to ISO 9001:2015, while improving their present quality management system (QMS)
Abstract — This paper discusses the management of the quality. system in a coach work company based on the ISO 9001 standar d, version 2015 and i t aims directin g and con trolli ng the pro ...
1.3 Research process. The general process of the thesis has been depicted in Image 1. The study branches into two separate flows. The first flow investigates the quality management system itself and the second one investigates process management methods used in the quality management system's context.
Implementation of Quality Management System ISO 9001 in A Telecom Network Operation Centre - A Case Study . Diana Ortiz-Rangel and Luis Rocha-Lona . ESCA Santo Tomas, Instituto Politecnico Nacional . Mexico City, Mexico . [email protected], [email protected] . Lila Margarita Bada-Carbajal . Instituto Tecnologico Superior de Alamo Temapache ...
ISO - International Organization for Standardization
ISO 9001 is a globally recognized standard for quality management systems. It is an important component of a well-rounded produc-tion management system. During a continuous improvement cycle, ISO 9001 helps to simplify the process, increase company performance, and boost efficiency. The case study shows how ISO 9001 was implemented in the ...
This case study outlines Quality Support Group's work with a small, Massachusetts-based machine shop to secure training grant funding and implement the ISO 9001:2015 Quality Management System. The 25 person operation, specializing in precision machining of metal and plastic parts, as well as metal fabrication, powder coating, and assembly ...
Written in plain English, Discover ISO 9001:2015Through Practical Examples will help you understand the relationship between your regular business operations and ISO 9001:2015, instead of implementing the standard purely to prove compliance. Title. Discover ISO 9001:2015 through practical examples.
PDCA model ISO 9001:2015. Plan: Establish objectives, resources required, customer and stakeholder requirements, organizational policies and identify risks and opportunities. Do: Implement what was planned. Check: Monitor and measure processes to establish performance against policies, objectives, requirements and planned activities and report ...
ISO 9001 Case Studies. Explore our ISO 9001 case studies to witness real-world examples of how companies worldwide have successfully implemented our products to establish custom quality management systems and achieve ISO 9001 certification. These case studies provide valuable insights into the practical application of ISO 9001 and offer ...
The paradigm shift - Learn from the industry leaders. The following is a case study of how Dell Computer implemented their ISO 9001:2000 transition. It was first implemented in their Asset Recovery Business (ARB), which had major challenges in meeting its strategic business goals. The directive was not merely to implement the 2000 revision ...
This study followed a case study of the implementation and impact of ISO 9001: 2008. Standard at the University of Nairobi. That methodology had four stages: design the. case study, conduct the ...
implementation of ISO 9001:2015 in various business sectors. The research was conducted by conducting a literature review on 19 articles related to the implementation of ISO 9001:2015 which were published in the last decade and then analyzed and drew conclusions. Based on the study of various previous studies in this paper, it
Investigate safety procedures, signs and personal protection equipment. Define and measure accidents and incidents, and set a target for the coming 3 years. Actions related to the strategic targets (3/3) Target 2.3. Develop at least one community project every year during 2014-2018. Planned actions.
ISO 9001 Quality Management case studies. ISO 9001 is the world's most recognized quality management standard. Implementing the standard can help you to continually monitor, manage and improve quality across all operations. This can help you save money, increase profit, win more business and satisfy more customers.
Its purpose is to provide deWnitions of terms and a basic explanation of the ISO 9000 standards. ISO 9001:2000 consolidates the former ISO 9001/9002/9003 standards into a single document and is the only standard to which certiWcation is currently assessed. ISO 9001:2000 is written for all types of organization, including service organizations.
The Implementation of a Quality Management System in Accordance with ISO 9001: 2015 Standard: A Case Study 266 Jr., 2018). Due to its high criticality, it represents one of the major obstacles for the implementation (Klute-Wenig and Refflinghaus, 2020). Since the implementation of ISO 9001 is a strategic decision (Sá et al., 2020), top
Assessment of ISO 9001:2015 implementation factors based on AHP: Case study in Brazilian automotive sector June 2018 International Journal of Quality & Reliability Management 35(4):00-00
Abstract. ISO 9001:2008 Quality Management Systems (QMS) standard was published as a standard that contains the requirements which an organization needs to fulfil to achieve customer satisfaction ...